集中处理站分离器磁翻板液位计冲洗装置的研制
返回列表发布日期:2020-01-04 16:54:11 |
摘 要:分离器在生产过程中,为防止液位计不准确而发生生产事故,处理站定期组织人员对液位计进行清洗维护,在清洗过程中,需要停用分离器、多人配合,还存在高空作业潜在的风险。我们通过研制分离器液位计冲洗装置,可以在不停用分离器情况下,一人15分钟就能完成,并消除了高空作业带来的风险,取得了良好的效果。
集中处理站是油田地面集输系统中重要的组成部分,是对若干计量站或接转站输送的混合液进行油气水分离、原油净化外输,天然气处理、污水处理的综合性站库。油气两相分离器是原油处理系统前端装置,分离器液位计目前广泛采用磁翻板液位计,磁翻板液位计在就地实时显示分离器液位的基础上,利用液位传感器可在中控室远程监测并与现场气动阀联动,实现分离器液位自动控制。液位计显示准确可靠是原油处理系统各项参数的基本保障。
1 问题的提出
1.1 液位计的结构及原理
磁翻板液位计由水包、磁性浮球、容纳浮球的腔体、翻板箱(红、白双色磁性小翻板)等组成。液位计腔体,通过液位计下游管线、法兰与水包组成一个连通器。上部开孔的水包安装在分离器底部,水包内加装的淡盐水是确保被测介质与显示机构相隔离。水包长时间在油水混合物里侵泡,会有油泥及其它等杂质沉积,极易造成液位计与水包的连通管线堵塞。若粘性较大的污油进入液位计腔体,容易使浮球上下移动卡阻,导致液位计显示不准确,可能造成分离器发生气线窜油等严重事故。(见图 1)
1.2 液位计的冲洗作业
为保证液位计液位显示准确可靠,集中处理站必须定期组织人员对液位计进行加水冲洗,以防液位计与水包的连通管线堵塞,并用淡盐水替换出水包内的污水及浮油,以确保液位计显示准确可靠。但在冲洗过程中存在以下问题:一是操作步骤繁琐、必须停用分离器,用时比较长;二是操作需攀登到 2 m 以上的高度进行作业;三是至少需要 4 人配合才能完成。
在液位计加水冲洗之前,首先由运行人员对该分离器进行停用。在做好各项安全措施后,操作人员架设梯子关闭液位计上下流阀门,然后打开液位计下部阀门对液位计进行放空后关闭,然后卸掉液位计上部堵头,一人扶梯子、一人递水、一人从上部堵头处往液位计腔体内加满水后上紧堵头,再打开液位计的上下流阀门将液位计腔体的水倒压至水包内。
集中处理站常用的磁翻板液位计腔体直径50 mm、高度 2 m,水包直径 300 mm、水包高度 0.3 m,由些可计算清洗并替换液泣计和水包内部的水所需要的用量。
液位计腔体体积:
经过计算,水包容积是液位计腔体容积的 5.4 倍,因此每次对液位计腔体加满水后,再将腔体的水倒压入水包的操作步骤至少需重复 6 次,每次的操作时间为 13 分钟左右,每清洗替换一台分离器液位计及水包的操作过程均在 1.5 小时以上,工作效率低,并且存在安全隐患。
2 分离器液位计冲洗装置的研制
2.1 设计思路
在分离器操作间内安装一套液位计冲洗置换装置,装置的压力平衡阀 5 通过管线与其中一台分离器液位计上游管线相连;装置的出水阀 6 通过出水管线分别与其它几台分离器液位计下游管线相连,一套液位计冲洗装置就可满足同一操作间内多台分离器液位计的冲洗要求。为了保障设备完整性,不对分离器及液位计主体结构进行更改和焊接,只在分离器与液位计上下游法兰之间加装三通和控制阀,分别与液位计冲洗置换装置的压力平衡阀与出水阀相连(见图 2)。
液位计冲洗置换时,先打开放空阀 4 及加水阀3 向装置内加满淡盐水,关闭加水阀 3、放空阀 4,然后打开装置的压力平衡阀 5,保证了装置内压力与分离器内压力相平衡;再打开出水阀 6 和待冲洗的液位计进水阀 7,利用液位差原理,就可以使装置内的水由液位计下游管线进入液位计水包,将水包内的介质置换到分离器内,完成液位计下游管线的冲洗检查和水包内介质的置换工作,从而达到冲洗检查液位计的目的(见图 3)
2.2 实施方案
经单位技术部门、安全部门审批,并出具技术变更方案,由专业队伍制作液位计冲洗置换装置。为了保证冲洗置换效果,装置主体盛水容量应大于一台液位计水包盛水容量;装置主体上部安装有放空阀、加水阀和压力平衡阀,下部安装有出水阀及低液位观察阀;冲洗装置安放在分离器操作间内,可满足多台分离器液位计冲洗条件;装置安装高度高于分离器液位计液位高度;为了便于向装置内部进行加水操作,配套设有作业平台。
2.2.1 冲洗装置主体结构
选用 φ219×7mm 的螺旋钢管制作,管材设计
承压 1.6MPa,远高于分离器工作压力(0.3MPa),保
障装置使用的安全性。
理论计算依据:
装置直径
D = φ219 × 7 = 219 - 7 × 2=205mm=0.205m (4)
参照相关规范:装置设计容量应大于水包本身容积量的 1.2~1.5 倍计算。
冲洗装置体积
装 置 容 量 V3(49.48L)大 于 液 位 计 水 包 V1 (21.195L)的盛水总量,即可将水包内部的介质全部替换清洗一遍。
2.2.2 装置管线、阀门等附件
选用 φ26×3 mm 无缝钢管、DN20 快速球阀等配件。管线、阀件设计承压 1.6 MPa,远大于分离器工作压力(0.3 MPa),保障了装置使用的安全性。快速球阀便于开关操作,可快速将装置内部的水压入水包内。
2.2.3 操作平台
选用钢管、钢板、角铁焊接牢固、安全可靠,便于人员操作。经过测量,分离器的工作液位距地面高度为 1.7 m,装置的安装高度只需大于分离器液位运行高度就能顺利压水冲洗。为了便于人员操作,结合人员 160~180 cm 身高,确定了操作平台高度为 1 m(见图 4)。
3 现场应用
3.1 作业效果
集中处理站分离器操作间安装液位计冲洗装置验收合格后,进行了多次现场操作验证,取得了较好的效果。
加水冲洗过程中,不用停用分离器,保证安全平稳生产;在作业平台上操作,消除了高处作业的风险;操作时间由原先的1.5小时降至目前的15分钟,提高了工作效率;由 4人操作减少为 1~2人操作,减少了作业人数,降低了员工的劳动强度。(见图5)。
3.2 效益评价
节约操作人工费用:
人工费用平均 180 元/天,每座百万吨级集中处理站平均设置 4 台分离器,每台分离器平均每月清洗置换液位计及水包一次,每次 4 人操作 1.5 小 时。每年每座处理站分离器清洗置换液位计及水包的人工费用为:
4 台×4 人/次×1.5 小时×12 次/台·年×180元/天·人÷8 小时/天=6 480 元/年;改造费用:人工费用 320 元+材料费用 730 元= 1 050 元;年节省操作费用:6480 元-1 050 元=5 430 元。
4 结果
分离器液位计清洗装置的研制,在液位计冲洗过程中,不用停用分离器,利用连通器压力平衡原理,完成了液位计及水包内污水的快速冲洗和置换,实现了冲洗过程中分离器液位的实时显示和远程控制,同时缩短了冲洗操作时间,减少了操作人数,降低员工的劳动强度,提高了工作效率,并将高处作业转变为常规作业,消除了高处作业在的安全隐患,为安全生产提供了保障,在油田地面集输系统具有很好的推广价值。
集中处理站是油田地面集输系统中重要的组成部分,是对若干计量站或接转站输送的混合液进行油气水分离、原油净化外输,天然气处理、污水处理的综合性站库。油气两相分离器是原油处理系统前端装置,分离器液位计目前广泛采用磁翻板液位计,磁翻板液位计在就地实时显示分离器液位的基础上,利用液位传感器可在中控室远程监测并与现场气动阀联动,实现分离器液位自动控制。液位计显示准确可靠是原油处理系统各项参数的基本保障。
1 问题的提出
1.1 液位计的结构及原理
磁翻板液位计由水包、磁性浮球、容纳浮球的腔体、翻板箱(红、白双色磁性小翻板)等组成。液位计腔体,通过液位计下游管线、法兰与水包组成一个连通器。上部开孔的水包安装在分离器底部,水包内加装的淡盐水是确保被测介质与显示机构相隔离。水包长时间在油水混合物里侵泡,会有油泥及其它等杂质沉积,极易造成液位计与水包的连通管线堵塞。若粘性较大的污油进入液位计腔体,容易使浮球上下移动卡阻,导致液位计显示不准确,可能造成分离器发生气线窜油等严重事故。(见图 1)

为保证液位计液位显示准确可靠,集中处理站必须定期组织人员对液位计进行加水冲洗,以防液位计与水包的连通管线堵塞,并用淡盐水替换出水包内的污水及浮油,以确保液位计显示准确可靠。但在冲洗过程中存在以下问题:一是操作步骤繁琐、必须停用分离器,用时比较长;二是操作需攀登到 2 m 以上的高度进行作业;三是至少需要 4 人配合才能完成。
在液位计加水冲洗之前,首先由运行人员对该分离器进行停用。在做好各项安全措施后,操作人员架设梯子关闭液位计上下流阀门,然后打开液位计下部阀门对液位计进行放空后关闭,然后卸掉液位计上部堵头,一人扶梯子、一人递水、一人从上部堵头处往液位计腔体内加满水后上紧堵头,再打开液位计的上下流阀门将液位计腔体的水倒压至水包内。
集中处理站常用的磁翻板液位计腔体直径50 mm、高度 2 m,水包直径 300 mm、水包高度 0.3 m,由些可计算清洗并替换液泣计和水包内部的水所需要的用量。
液位计腔体体积:

2 分离器液位计冲洗装置的研制
2.1 设计思路
在分离器操作间内安装一套液位计冲洗置换装置,装置的压力平衡阀 5 通过管线与其中一台分离器液位计上游管线相连;装置的出水阀 6 通过出水管线分别与其它几台分离器液位计下游管线相连,一套液位计冲洗装置就可满足同一操作间内多台分离器液位计的冲洗要求。为了保障设备完整性,不对分离器及液位计主体结构进行更改和焊接,只在分离器与液位计上下游法兰之间加装三通和控制阀,分别与液位计冲洗置换装置的压力平衡阀与出水阀相连(见图 2)。
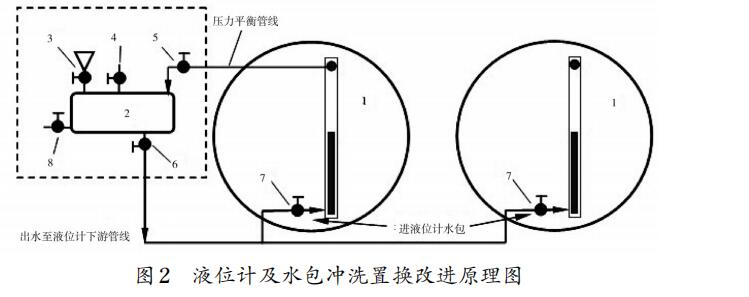

经单位技术部门、安全部门审批,并出具技术变更方案,由专业队伍制作液位计冲洗置换装置。为了保证冲洗置换效果,装置主体盛水容量应大于一台液位计水包盛水容量;装置主体上部安装有放空阀、加水阀和压力平衡阀,下部安装有出水阀及低液位观察阀;冲洗装置安放在分离器操作间内,可满足多台分离器液位计冲洗条件;装置安装高度高于分离器液位计液位高度;为了便于向装置内部进行加水操作,配套设有作业平台。
2.2.1 冲洗装置主体结构
选用 φ219×7mm 的螺旋钢管制作,管材设计
承压 1.6MPa,远高于分离器工作压力(0.3MPa),保
障装置使用的安全性。
理论计算依据:
装置直径
D = φ219 × 7 = 219 - 7 × 2=205mm=0.205m (4)
参照相关规范:装置设计容量应大于水包本身容积量的 1.2~1.5 倍计算。
冲洗装置体积

2.2.2 装置管线、阀门等附件
选用 φ26×3 mm 无缝钢管、DN20 快速球阀等配件。管线、阀件设计承压 1.6 MPa,远大于分离器工作压力(0.3 MPa),保障了装置使用的安全性。快速球阀便于开关操作,可快速将装置内部的水压入水包内。
2.2.3 操作平台
选用钢管、钢板、角铁焊接牢固、安全可靠,便于人员操作。经过测量,分离器的工作液位距地面高度为 1.7 m,装置的安装高度只需大于分离器液位运行高度就能顺利压水冲洗。为了便于人员操作,结合人员 160~180 cm 身高,确定了操作平台高度为 1 m(见图 4)。

3.1 作业效果
集中处理站分离器操作间安装液位计冲洗装置验收合格后,进行了多次现场操作验证,取得了较好的效果。
加水冲洗过程中,不用停用分离器,保证安全平稳生产;在作业平台上操作,消除了高处作业的风险;操作时间由原先的1.5小时降至目前的15分钟,提高了工作效率;由 4人操作减少为 1~2人操作,减少了作业人数,降低了员工的劳动强度。(见图5)。

节约操作人工费用:
人工费用平均 180 元/天,每座百万吨级集中处理站平均设置 4 台分离器,每台分离器平均每月清洗置换液位计及水包一次,每次 4 人操作 1.5 小 时。每年每座处理站分离器清洗置换液位计及水包的人工费用为:
4 台×4 人/次×1.5 小时×12 次/台·年×180元/天·人÷8 小时/天=6 480 元/年;改造费用:人工费用 320 元+材料费用 730 元= 1 050 元;年节省操作费用:6480 元-1 050 元=5 430 元。
4 结果
分离器液位计清洗装置的研制,在液位计冲洗过程中,不用停用分离器,利用连通器压力平衡原理,完成了液位计及水包内污水的快速冲洗和置换,实现了冲洗过程中分离器液位的实时显示和远程控制,同时缩短了冲洗操作时间,减少了操作人数,降低员工的劳动强度,提高了工作效率,并将高处作业转变为常规作业,消除了高处作业在的安全隐患,为安全生产提供了保障,在油田地面集输系统具有很好的推广价值。